Case study: Blister packaging insert
Application at the customer
Blister pack with a desiccant bag containing 1 g silica gel on top is packed airtight in an aluminum composite bag. Several of these aluminum bags are stacked in a cardboard box.
The challenge
The customer processes our desiccant bags on a roll with a high-speed bag separator in a non-stop operation. They are fed to the processing plant at more than 200 cycles per minute.
Standard desiccant sachets are significantly smaller than the blister pack and are bulky. As a result, the tower of stacked aluminum bags becomes wobbly and slanted and can no longer be automatically pushed into the box.
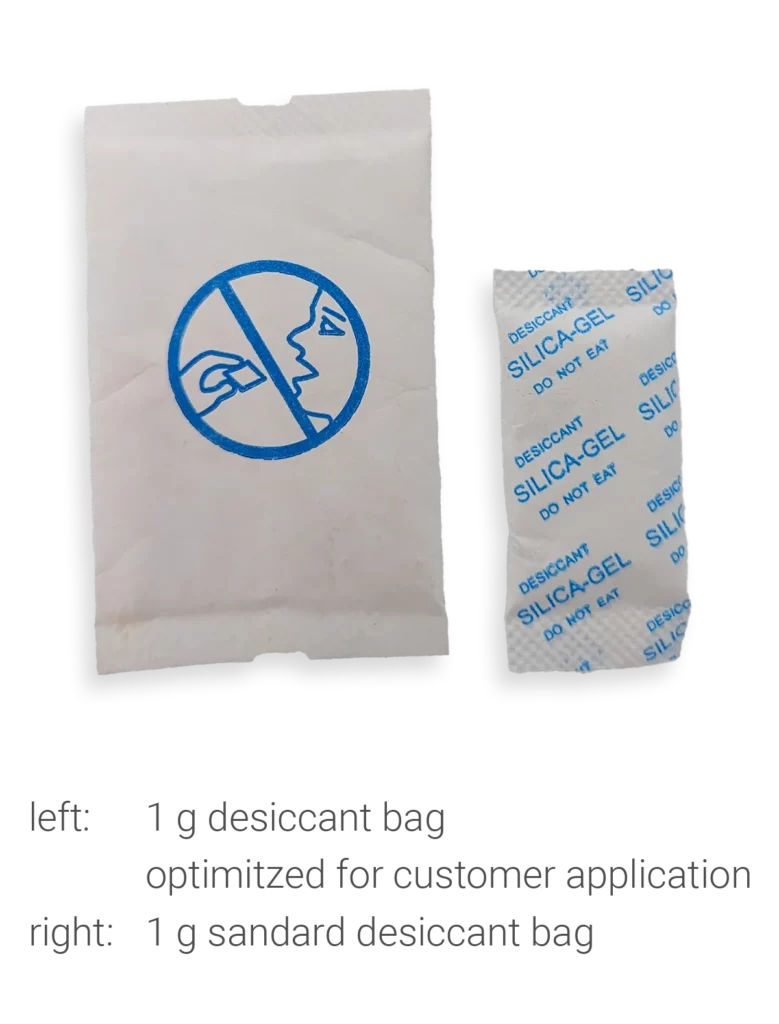
Process
To develop the optimum product for the application described, the ThoMar project manager visited the customer's premises to get a detailed picture of the processing machines. Adapted samples were then made available for testing.
Solution
Part 1: Adjusting the desiccant bag
Use of a larger desiccant bag that is very flat. Very fine silica gel is used for this, which is evenly distributed in the bag.
Part 2: Adjusting the winding
The bags are wound very tightly into a bag chain so that the individual bags remain flat.
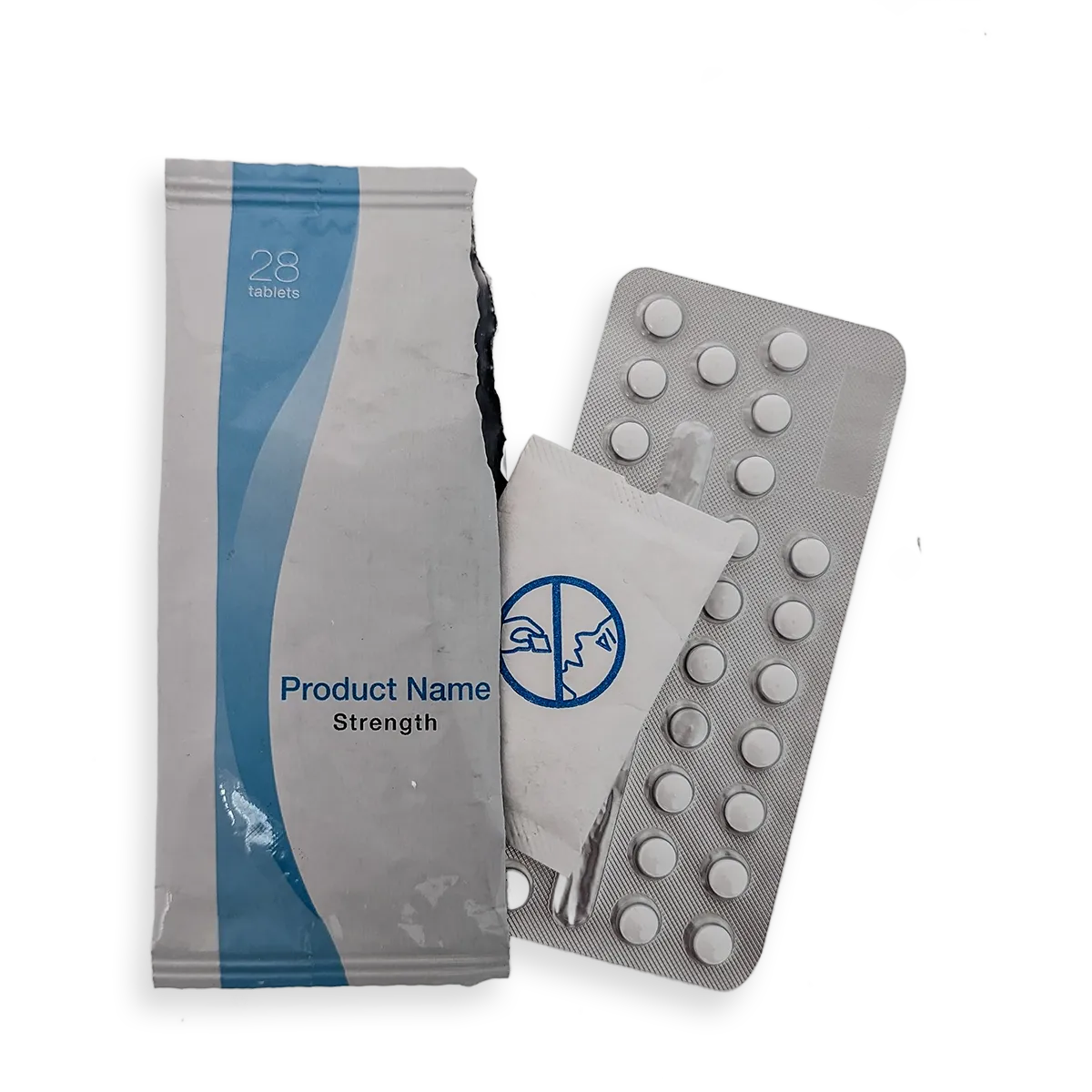